Introduction
Diesel generators play a crucial role in providing backup power in various industries, including manufacturing, healthcare, telecommunications, and more. These generators are essential for ensuring uninterrupted operations during power outages or emergencies. To maintain their reliability and safety, it is imperative to conduct regular certification inspections. This article explores the significance of diesel generator certification inspections, the inspection process, key components to assess, common issues found during inspections, and best practices for ensuring compliance and optimal performance.
Importance of Diesel Generator Certification Inspection
Certification inspections are vital for diesel generators to ensure that they meet regulatory requirements, industry standards, and safety guidelines. These inspections help in verifying the proper functioning of the generator and its components, identifying any potential issues or defects, and ensuring that the generator is ready to perform when needed. By conducting regular certification inspections, organizations can minimize the risk of unexpected failures, costly downtime, and safety hazards.
Moreover, compliance with certification requirements is often a regulatory mandate for many industries. Failing to adhere to these requirements can result in fines, penalties, or even legal consequences. Therefore, staying proactive with certification inspections is essential for maintaining compliance and demonstrating a commitment to safety and operational excellence.
The Inspection Process
The diesel generator certification inspection process typically involves a thorough assessment of various components and systems to ensure their proper functioning and compliance with relevant standards. The process may vary depending on the size and type of the generator, but it generally includes the following steps:
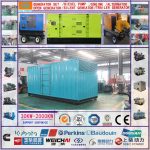
1. Visual Inspection: The inspection starts with a visual assessment of the generator, looking for signs of wear, corrosion, leaks, or any visible damage. This includes inspecting the engine, fuel system, cooling system, exhaust system, electrical components, and other critical parts.
2. Functional Testing: Functional tests are conducted to evaluate the performance of the generator under load conditions. This may involve running the generator to assess its startup time, voltage output, frequency stability, and response to load changes.
3. Electrical Testing: Electrical measurements are taken to verify the integrity of the generator's electrical system, including voltage levels, current ratings, insulation resistance, grounding continuity, and protective device operation.
4. Fuel System Inspection: The fuel system, including fuel tanks, filters, lines, and injectors, is inspected to ensure proper fuel delivery, filtration, and contamination prevention. Fuel quality and storage conditions are also assessed.
5. Cooling System Evaluation: The cooling system, comprising the radiator, coolant, hoses, and thermostats, is examined to ensure efficient heat dissipation and temperature regulation. Coolant levels, condition, and circulation are critical factors in preventing overheating.
6. Exhaust System Check: The exhaust system is inspected for leaks, corrosion, proper ventilation, and compliance with emission standards. Exhaust gases should be safely directed away from the generator and the facility to prevent health hazards.
7. Control System Assessment: The generator's control panel, sensors, gauges, alarms, and safety features are tested to ensure proper operation and responsiveness. Emergency shutdown procedures are also verified during the inspection.
8. Load Bank Testing: In some cases, load bank testing may be used to simulate real-world operating conditions and evaluate the generator's performance under different load levels. This test helps in identifying potential issues related to load capacity and voltage regulation.
Key Components to Assess
During a diesel generator certification inspection, several key components and systems must be thoroughly assessed to ensure the generator's reliability and compliance. These components include:
1. Engine: The engine is the heart of the generator and must be in optimal condition for reliable operation. Components such as pistons, cylinders, valves, fuel injectors, and turbochargers should be inspected for wear, leaks, and proper lubrication.
2. Alternator: The alternator is responsible for generating electrical power and must be inspected for proper alignment, insulation integrity, winding resistance, and voltage output consistency. Any signs of overheating or electrical faults should be addressed promptly.
3. Cooling System: The cooling system plays a critical role in maintaining the engine's operating temperature within safe limits. Radiators, coolant levels, water pumps, and hoses should be inspected for leaks, blockages, and efficient coolant circulation.
4. https://www.lkpowerplant.com/product/emergency-use-diesel-generator-set-for-150kw-380-v-three-phase-large/ : The fuel system ensures the reliable supply of diesel fuel to the engine for combustion. Fuel tanks, filters, lines, injectors, and fuel quality should be checked to prevent fuel contamination, blockages, or inadequate fuel delivery.
5. Exhaust System: The exhaust system is essential for safe emission of combustion gases away from the generator and the facility. Exhaust pipes, mufflers, silencers, and emission control devices should be inspected for leaks, corrosion, and compliance with environmental regulations.
6. Control System: The control panel and associated components control the generator's operations, monitor parameters, and initiate safety shutdowns when necessary. Control systems, sensors, alarms, and safety features should be tested for accuracy and responsiveness.
7. Electrical System: The electrical system includes components such as wiring, connections, breakers, switches, and protective devices. Insulation resistance, grounding continuity, voltage levels, and current ratings should be verified to prevent electrical faults and hazards.
8. Batteries: The generator's starting batteries play a crucial role in initiating the engine startup process. Battery condition, electrolyte levels, terminal connections, and charging systems should be inspected to ensure reliable starting performance.
Common Issues Found During Inspections
During diesel generator certification inspections, several common issues and defects may be identified, indicating the need for maintenance or repairs. Some of the common issues found during inspections include:
1. Fuel Contamination: Diesel fuel contamination with water, sediment, or microbial growth can lead to fuel system clogging, injector damage, and engine performance issues. Regular fuel quality checks and filtration are essential to prevent contamination.
2. Cooling System Leaks: Coolant leaks from hoses, radiators, water pumps, or gaskets can result in overheating, engine damage, and reduced efficiency. Detecting and repairing cooling system leaks is crucial for maintaining proper temperature control.
3. Exhaust System Corrosion: Corrosion in exhaust pipes, mufflers, or silencers can cause exhaust leaks, noise pollution, and safety hazards. Regular inspection and maintenance of the exhaust system are necessary to prevent corrosion and ensure compliance with emission standards.
4. Electrical Faults: Wiring faults, loose connections, insulation breakdown, or overload conditions can result in electrical malfunctions, short circuits, and power outages. Electrical testing and preventive maintenance help in identifying and resolving electrical issues.
5. Battery Failure: Weak or discharged starting batteries can lead to engine startup failures and operational downtime. Regular battery testing, charging, and replacement are essential for ensuring reliable engine starting performance.
6. Overheating: Engine overheating due to cooling system issues, coolant leaks, or improper ventilation can cause engine damage and reduced efficiency. Monitoring coolant levels, circulation, and radiator performance helps prevent overheating.
7. Voltage Instability: Voltage fluctuations, under- or overvoltage conditions, or frequency variations can affect the generator's electrical output and connected loads. Voltage regulation tests and adjustments are necessary to maintain stable power supply.
8. Control System Errors: Malfunctioning control panels, sensors, alarms, or safety features can compromise the generator's operational integrity and safety. Regular testing and calibration of control systems help in detecting and correcting errors.
Best Practices for Ensuring Compliance and Optimal Performance
To ensure compliance with certification requirements and maintain optimal performance, organizations should follow best practices for diesel generator maintenance and inspection. Some of the best practices include:
1. Regular Inspection Schedule: Establish a routine inspection schedule based on manufacturer recommendations, industry standards, and regulatory requirements. Conduct periodic inspections to identify issues early and address them promptly.
2. Qualified Inspection Personnel: Ensure that the inspection personnel are trained, certified, and experienced in diesel generator maintenance and inspection. Qualified technicians can accurately assess the generator's condition and perform necessary repairs.
3. Documentation and Record-Keeping: Maintain detailed records of inspection results, maintenance activities, repairs, and compliance documentation. Proper documentation helps in tracking the generator's history, identifying trends, and demonstrating compliance during audits.
4. Preventive Maintenance Program: Implement a proactive maintenance program that includes regular servicing, lubrication, filter replacements, and system checks. Preventive maintenance helps in preventing unexpected failures and extending the generator's lifespan.
5. Load Testing: Conduct load bank testing periodically to simulate real-world operating conditions and verify the generator's performance under varying load levels. Load testing helps in identifying capacity issues, voltage regulation problems, and fuel efficiency.
6. Emergency Preparedness: Develop and practice emergency response plans for generator failures, power outages, and safety incidents. Ensure that personnel are trained in shutdown procedures, evacuation protocols, and emergency communications.
7. Compliance Audits: Periodically review and audit the diesel generator certification inspection reports, maintenance logs, and compliance documentation. Verify that the generator meets regulatory requirements, industry standards, and safety guidelines.
8. Continuous Improvement: Continuously monitor and evaluate the generator's performance, maintenance practices, and inspection results. Identify areas for improvement, implement corrective actions, and update maintenance procedures to enhance reliability and compliance.
Conclusion
In conclusion, diesel generator certification inspections are essential for ensuring compliance, reliability, and safety in various industries that rely on backup power systems. By following a systematic inspection process, assessing key components, identifying common issues, and implementing best practices for maintenance and compliance, organizations can minimize the risk of unexpected failures, downtime, and safety hazards associated with diesel generators. Investing in proper inspection and maintenance of diesel generators is a proactive approach to safeguarding operations, protecting assets, and demonstrating a commitment to operational excellence.